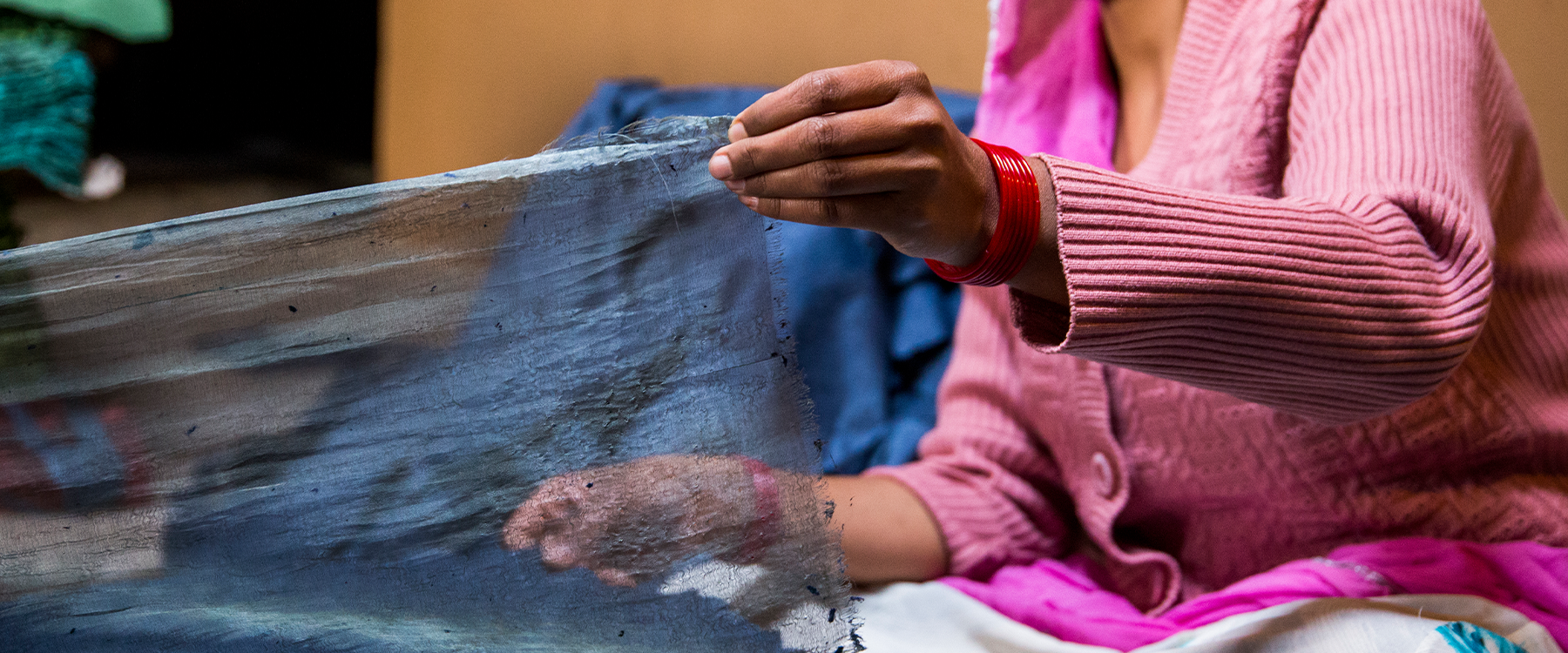
“Today, we make one of the most regenerative papers in the world. Our 100% natural, chemical-free handmade products actually enhance the local environment and local community.”
- Vijendra, Founder
Process from Start to Finish
Still have questions? Visit our FAQ page for more information about how we make paper from poo.
Watch the Elephant Poo Paper process from start to finish.
-
Our elephants are key to the process and they deserve the best. Vijendra takes them greens from the market – which improves their diets and the raw material we use for making paper.
-
After feeding the elephants, Vijendra collects dung from the local elephant camps and loads it onto his truck to bring back here.
-
Elephants have an inefficient digestive system so their poop contains a lot of unprocessed plant fibre. By washing the dung two or three times, everything gets flushed away except for the fibre – the part we use.
This stage in the process uses a lot of water but it’s anything but wasteful.
We collect the nutrient-rich wastewater and give it to local farmers to use on their fields. The water is so rich in nutrients it means they don’t need to use chemical fertilisers to enrich their soil.
-
After washing the dung, we mix salt and baking soda into boiling water and add the plant fibre.
The mixture is boiled for two to three hours. The result: odour free sterilised fibre.
-
Due to the large size of the fibres, the first step is to beat the washed dung into a pulp.
The mixture is circulated by a simple grinding head sitting in an oval track tub. This refines the fibres, making them suitable for paper making.
The team then add cotton waste (recycling scrap material from local textile shops) to create a final mixture that is 75% elephant dung and 25% recycled cotton.
The cotton is added to the dung to bind the fibres so that our paper is as strong as normal paper.
In this step, natural dyes, which come from a variety of plants such as tesu, night wood, and pomegranate skins, can be added to create the desired colour.
-
Next, Viejndra adds a scoop of the mixture – measured only by eye and years of experience – to a bath where the sheet of paper will be created.
-
A two-person team submerges a screen fixed to a wooden frame into the bath. They churn the mixture for a few seconds to make sure that the fibres are evenly dispersed. Then they steadily raise the screen, which causes an even layer of fibres to become trapped to it while the water passes through.
The next step is to fix fabric to the top of the newly created sheet, which is then flipped over onto a stack of already created sheets. The fabric ensures that the sheets of paper don’t stick together.
-
To remove the excess water from the sheets of paper, the stack (of about 500 sheets) is put into a press to squeeze out most of the water. The immense pressure reduces the height of the stack from three feet to a little over one.
The fabrics are taken out from between the layers of paper and the sheets are hung overhead to dry for 14 to 18 hours.
-
And finally, the paper is ‘calendered’ to make it smooth.
This entails feeding paper and metal sheets alternately into a large steel roller. The pressure flattens it out and gets rid of any unwanted texture.
The stack is only put through the roller once because too much pressure will blacken the fibres. Calendaring makes the paper uniform and easy to write on.
-
From here, the paper is sent to a local finishing shop where a recycled cotton backing is added to it to ensure it’s strong enough for multiple uses.
To make our bags, the paper is shaped using a custom-made die before it’s folded and glued together by one of our co-workers. They then add grommets and string handles to finish the bag off. And voilà!